Foto: Pixabay
Ressourcen schonen, Energie sparen, CO₂-Ausstoß reduzieren: Auf dem Weg zu mehr Nachhaltigkeit und Klimaschutz spielt die Industrie eine Schlüsselrolle. Digitalisierung ist der wesentliche Hebel, um diese Ziele zu erreichen. Gefragt ist hierbei auch das Know-how der Armaturenbranche.
Ein Beitrag von Michael Vehreschild.
Eine aktuelle, repräsentative Befragung im Auftrag des Digitalverbands Bitkom (Bundesverband Informationswirtschaft, Telekommunikation und neue Medien e.V.) stellt die Bedeutung digitaler Anwendungen für mehr Klimaschutz heraus. Demnach sagen 8 von 10 Unternehmen (81 Prozent), dass Industrie 4.0 zu einer nachhaltigen Produktion beiträgt. Befragt wurden rund 550 Industrieunternehmen in Deutschland ab 100 Beschäftigten.
Mit Digitalisierung den Herausforderungen stellen
Gleichzeitig betonen 91 Prozent, dass Industrie 4.0 unverzichtbar ist, um im internationalen Wettbewerb bestehen zu können. 6 von 10 Unternehmen sagen, dass die Arbeit weniger fehleranfällig wird (61 Prozent) und sich konventionelle Geschäftsmodelle verändern werden (58 Prozent). „Durch eine konsequente Digitalisierung kann die deutsche Industrie sich zwei dringlichen Herausforderungen zugleich stellen: Digitalisierung macht die Unternehmen nachhaltiger und wettbewerbsfähiger“, sagt Christina Raab, Mitglied im Bitkom-Präsidium.
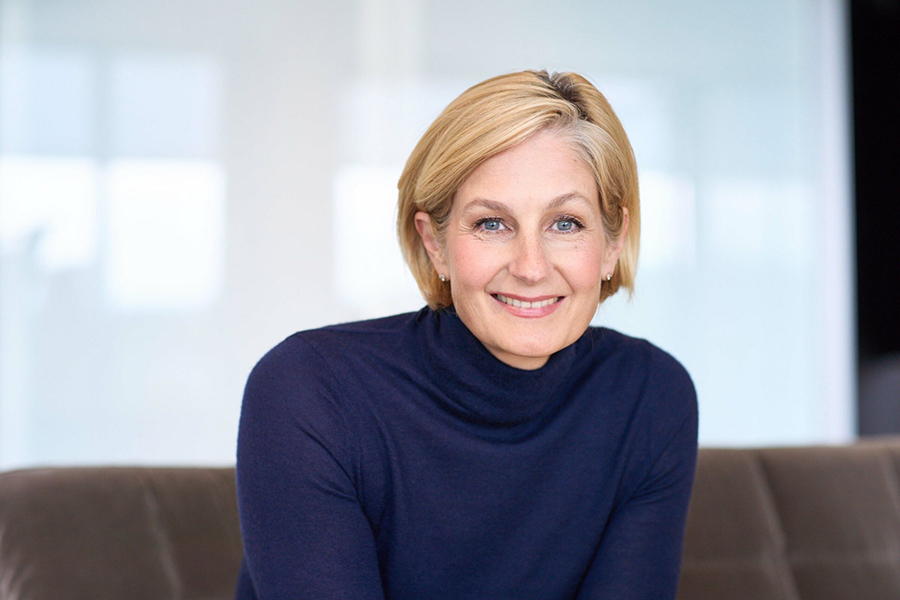
Großes Potenzial bietet die Digitalisierung der Industrie in der Reduktion von CO₂-Emissionen. So können im Jahr 2030 bei einem beschleunigten Einsatz digitaler Technologien allein in Deutschland bis zu 64 Millionen Tonnen CO₂ eingespart werden – das sind 17 Prozent der insgesamt geplanten CO₂-Einsparungen im Rahmen des Klimaziels 2030. Das zeigt die Bitkom-Studie „Klimaeffekte der Digitalisierung“. Demnach kann der Einsatz von digitalen Zwillingen, also die Simulation und Optimierung von physikalischen Produkten oder Prozessen, 33 Millionen Tonnen CO₂ einsparen. Weitere 31 Millionen Tonnen können durch verstärkte Automatisierung in der Produktion vermieden werden, indem digitale Technologien manuelle Eingriffe und den Materialeinsatz reduzieren sowie Prozesse optimieren.
9 von 10 Unternehmen setzen auf Industrie 4.0
65 Prozent der Industrieunternehmen ab 100 Beschäftigten nutzen derzeit spezielle Anwendungen für Industrie 4.0 und weitere 25 Prozent planen den Einsatz. Raab: „Industrie 4.0 ist im produzierenden Gewerbe angekommen. Insgesamt setzen 90 Prozent der Unternehmen auf Industrie 4.0 – und investieren dafür rund 6 Prozent ihres gesamten Jahresumsatzes.“ Vergangenes Jahr waren es nach Bitkom-Angaben mit 83 Prozent noch etwas weniger, im Jahr 2019 waren es sogar erst 74 Prozent. Nur 8 Prozent planen derzeit keinen Einsatz spezieller Anwendungen, können sich aber vorstellen, dies in Zukunft zu tun. Für ausnahmslos alle der befragten Unternehmen ist Industrie 4.0 heute ein Thema. „Die Corona-Pandemie hat der deutschen Industrie einen dauerhaften Digitalisierungsschub gegeben“, so Raab.

Künstliche Intelligenz zählt heute zu den Schlüsseltechnologien in der Industrie. In fast 4 von 10 Unternehmen (38 Prozent) hat sie Anwendung gefunden – 66 Prozent von ihnen nutzen KI in der Produktion zur Automatisierung von Prozessen, 64 Prozent für die Datenanalyse bei der Prozessüberwachung, 35 Prozent wenden beide Einsatzmöglichkeiten an. Konkrete Pläne für den Einsatz von KI haben 17 Prozent der Unternehmen, 18 Prozent diskutieren darüber.
Bedeutung digitaler Zwillinge steigt
Digitale Zwillinge werden in jedem dritten Unternehmen (33 Prozent) eingesetzt. Ein weiteres Fünftel (19 Prozent) plant die Nutzung und 16 Prozent diskutieren dies. „Digitale Zwillinge sind digitale Kopien von Objekten der realen Welt – von Produkten und Maschinen bis zu ganzen Fabriken. Dank ihrer Hilfe lassen sich Produktions- und Wartungsprozesse massiv beschleunigen und im alltäglichen Einsatz fortlaufend optimieren“, erklärt Raab. Die Bedeutung von digitalen Zwillingen wird mittelfristig weiter zunehmen. So ist eine große Mehrheit der Unternehmen (82 Prozent) der Meinung, dass der Einsatz digitaler Zwillinge in den kommenden fünf Jahren ansteigen wird.
Potenziale von IoT-Plattformen
IoT-Plattformen, mit denen Daten, Produkte, Maschinen oder Prozesse vernetzt werden können, setzen 35 Prozent der produzierenden Unternehmen ein und fast genauso viele (30 Prozent) planen dies. Für lediglich 14 Prozent sind IoT-Plattformen kein Thema, bei 19 Prozent steht der Einsatz zur Diskussion. Fast jedes Zweite (49 Prozent) sieht die größten Potenziale bei so genanntem Remote Monitoring – also der Fernüberwachung – und bei Echtzeit-Einblicken in die Herstellungsprozesse. 42 Prozent schätzen die Beschleunigung von Prozessen. 39 Prozent sehen Potenziale in der Predictive Maintenance. IoT-Plattformen helfen auch bei der Erreichung übergeordneter betrieblicher Ziele wie der Umsatzsteigerung (40 Prozent), der Qualitätsverbesserung (36 Prozent) und der Kostensenkung (31 Prozent).
Fachkräfte profitieren von Industrie 4.0
Der zunehmende Einsatz digitaler Technologien im industriellen Umfeld verändert auch den Arbeitsmarkt. So erwarten 7 von 10 Unternehmen (71 Prozent), dass durch Industrie 4.0 neue Arbeitsplätze für gut ausgebildete Fachkräfte entstehen. Im Vorjahr meinten dies erst 57 Prozent. Auf diesen Wandel stellt sich die Industrie jetzt ein. Mehr als drei Viertel (77 Prozent) der Industrieunternehmen investieren in die Weiterbildung ihrer Mitarbeitenden rund um Industrie 4.0 (2021: 68 Prozent). Zugleich meinen aber auch 61 Prozent, dass Arbeitsplätze für gering Qualifizierte wegfallen werden.
Mittelstand: Nachholbedarf bei Industrie 4.0
Immerhin 39 Prozent der deutschen Industrieunternehmen sehen sich als Vorreiter der Industrie 4.0. Andererseits gruppiert sich jedes Zweite (51 Prozent) als Nachzügler. 7 Prozent der Unternehmen fühlen sich abgehängt. Den größten Nachholbedarf hat der Mittelstand. So bezeichnen sich 58 Prozent der Unternehmen mit 100 bis 499 Beschäftigten als Nachzügler und nur 30 Prozent als Vorreiter. Unter den großen Unternehmen ab 500 Mitarbeitenden ist es umgekehrt: Lediglich 37 Prozent sehen sich als Nachzügler, mehr als die Hälfte (54 Prozent) als Vorreiter.
Das größte Hemmnis, Industrie 4.0 zu etablieren, sind nach Selbstauskunft der Unternehmen fehlende finanzielle Mittel (81 Prozent). Aber auch die Anforderungen an den Datenschutz empfinden zwei Drittel (67 Prozent) als Hemmnis. 61 Prozent identifizieren Anforderungen an die IT-Sicherheit als Problem und für 58 Prozent ist das Thema zu komplex.
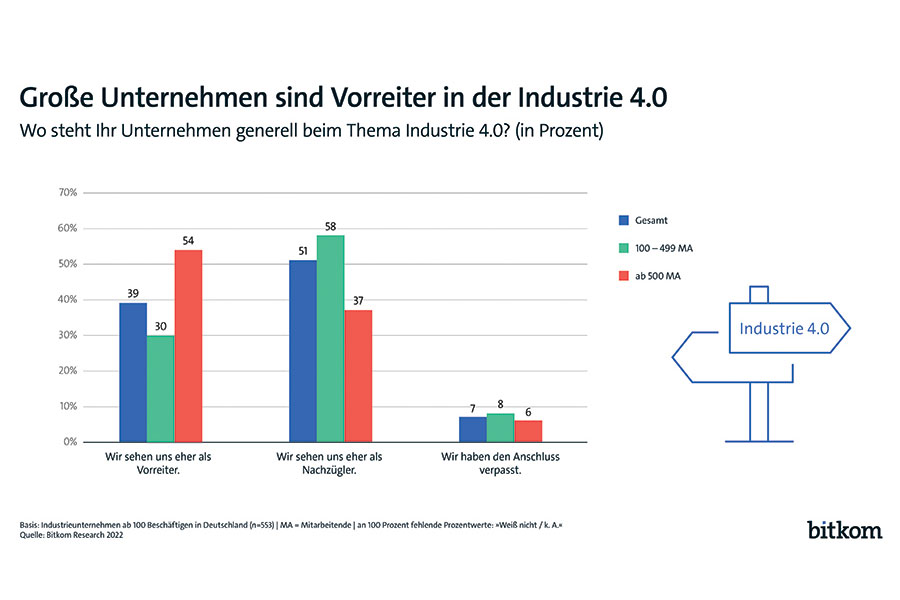
Regulierung, Förderung und Bildungsangebote
Auf dem digitalen Wunschzettel der Unternehmen stehen steuerliche Maßnahmen ganz oben. 84 Prozent fordern steuerliche Impulse, um Investitionen in die Industrie 4.0 anzuschieben. Ähnliche viele – 82 Prozent – wünschen sich mehr Rechtssicherheit beim Datenaustausch mit anderen Unternehmen. 44 Prozent plädieren für die Etablierung von Standards für Industrie-4.0-Anwendungen. Etwa 6 von 10 Unternehmen wollen einen schnelleren Bewilligungsprozess von Förderanträgen (61 Prozent) und mehr als die Hälfte (52 Prozent) plädiert für den Ausbau von FuE-Förderprogrammen für Hochschulen und Forschungseinrichtungen.
Im Bildungsbereich wünschen sich 59 Prozent Weiterbildungsangebote und die Integration von Industrie-4.0-Themen in Ausbildung und Studium. 55 Prozent möchten Programme zur Aus- und Weiterbildung von Fachkräften rund um Industrie 4.0 und etwa genauso viele (54 Prozent) mehr Informations- und Beratungsangebote für Unternehmen. „Digitalisierung ist der Schlüssel für Wettbewerbsfähigkeit und Nachhaltigkeit der deutschen Industrie“, so Raab.
Durchblick im Dschungel der Industrie 4.0 will der Bitkom mit einem neuen „Industrie-4.0-Digitalisierungsradar“ schaffen. Darin werden relevante Technologien und Einsatzfelder aufgezeigt.
Armaturen- und Antriebsbranche investiert in Digitalisierung
Dass Innovationen in der Digitalisierung unverzichtbar sind, ist der Armaturen- und Antriebsbranche längst bewusst – sie hat bereits in den vergangenen Jahren entsprechend investiert. Aus gutem Grund, denn die Digitalisierung erlaube dem Kunden eine möglichst genaue Ausrichtung der Produkte auf seine spezifische Anwendung. „So können Prozesse flexibel, effizient und optimal gestaltet werden. Mit unseren Produkten unterstützen wir diese Entwicklung und ermöglichen eine einfache Implementierung der Stellantriebe in die Prozesse“, erklärt beispielsweise erklärt Stefan Radermacher, Vertriebsleiter der ARIS Stellantriebe GmbH. Moderne Stellantriebe erlauben eine flexible Programmierung von diversen Parametern durch den Kunden. Stefan Radermacher: „Außerdem können Software-Erweiterungen durch digitale Freischaltcodes aufgespielt werden – ohne den Versand von Hardware. Es gibt hier also keine Lieferzeiten.“
Ein weiteres wichtiges, aktuelles Thema, das im Fokus vieler Unternehmen steht, ist die Nachhaltigkeit und Effizienz. „ARIS Stellantriebe werden mit hochwertigen, robusten und nachhaltigen Komponenten hergestellt.“ Die Einhaltung der RoHS-Richtlinien sei dabei eine Selbstverständlichkeit. „Auf beides achten wir schon in den frühesten Stadien der Entwicklung.“ Dies spiegele sich in einer besonders langen Nutzungsdauer und Zuverlässigkeit wider. Des Weiteren sollten Stellantriebe einen möglichst geringen Energieverbrauch haben, also eine hohe Energieeffizienz, „was unsere Stellantriebe schon seit Langem auszeichnet“.
Datenaufbereitung in der Armaturenbranche ist wegweisend
Nimmt man die Entwicklung beim pneumatischen Stellantrieb in den Blick, wird schnell klar, „dass hier die Digitalisierung bisher in Anbauteile ausgelagert wurde“, erläutert Mark Schmidt, Geschäftsführer von Air Torque. Dies habe den Vorteil der einfachen Austauschbarkeit, bei maximaler Standardisierung. Mark Schmidt: „Der Nutzen bleibt gleich dem der integrierten Variante – vom Teach-in bis zur vorausschauenden, kostengünstigen Instandhaltung.“ Gleichwohl gebe es mittlerweile auch bei den pneumatischen Lösungen All-in-One Produkte. „Bleibt abzuwarten, für was sich der Markt entscheidet.“

Wegweisend für die Durchsetzung dieser Trends wird aus Sicht des Air Torque-Geschäftsführers die Datenaufbereitung und Speicherung der Vielzahl an Messungen sein: angefangen bei der Standardisierung bis hin zur Datenhoheit und Sicherheit, lokal oder in einer Cloud bei einem Provider oder Hersteller.
Keine Frage – die Armaturen- und Antriebsbranche wird ein wichtiger Katalysator für die zunehmende Digitalisierung und den Kurs auf Industrie 4.0 sein.
Über den Artikel der Woche
Jede Woche beleuchten wir im Artikel der Woche ein spannendes Thema für die Armaturenbranche. Weitere Artikel finden Sie auch in unserer Zeitschrift Armaturen Welt. Um diese und viele weitere Artikel (fast) monatlich zu lesen, abonnieren Sie unsere Zeitschrift (erhältlich in Print und digital).
Möchten Sie als Autor mitwirken? Bitte kontaktieren Sie Michael Vehreschild.
Jede Woche teilen wir einen neuen Artikel mit unserer Armaturen Community. Machen Sie mit und lassen Sie uns Ihren Artikel auf Armaturen Welt online und in gedruckter Form veröffentlichen.
Alle Bilder wurden vor der COVID-19-Pandemie bzw. unter Einhaltung der Abstandsregeln aufgenommen.